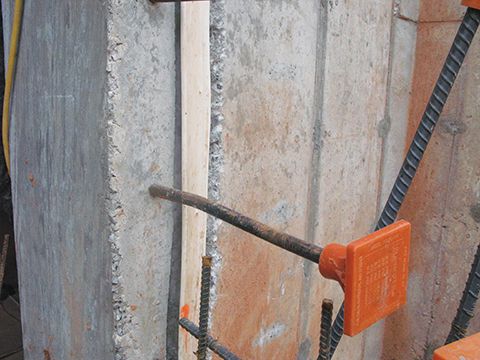
Thermoplastic and rubber extrusions
To accommodate varying hydrostatic pressure and movement, most thermoplastic and rubber waterstops come in different extruded profiles, widths, and thicknesses. For years, the most widely used waterstops were those anchored by having a dumbbell shape at each end, which provided a ‘cork-in-the-bottle’ seal when the joint opens. However, American Concrete Institute (ACI) 504R, Guide to Joint Sealants for Concrete Structures, reports this seal is ineffective at small joint movements, and at wider movements the waterstop
is placed in considerable tension. To overcome these issues, waterstop manufacturers developed profiles with multiple raised ribs to provide improved anchoring and sealing performance.
Both ribbed and dumbbell waterstops are available with flat-web or bulbed centers. They typically are available in 15.2-m (50-ft) rolls, in widths of 102 to 305 mm (4 to 12 in.) and thicknesses of 5 to 13 mm (3/16 to ½ in.). Flat-web waterstops are recommended for use in construction and contraction joints where little or no movement is expected. Since the center bulb flexes to accommodate both shear and transverse movements, these waterstops can be used in expansion, contraction, or construction joints. The center bulbs come in various sizes to accommodate differing amounts of joint movement, with larger-diameter center bulbs suitable for greater joint movements.
Some ribbed waterstops have a center bulb with a thin tear-web on one side that ruptures upon joint expansion. With the tear-web broken, the center bulb can open up to the extended width of the joint without stressing the embedded ribbed sections. The tear-web keeps concrete out of the center bulb during concrete placement. Manufacturers recommend using tear-web waterstops where large movement is expected. They should be installed so the tear-web side faces the direction of positive pressure.
While rubber thermoset waterstops have excellent mechanical properties (i.e. high tensile strength and good elongation), they are difficult to field-fabricate as the rubber is vulcanized, meaning it has already taken a ‘set’ (i.e. thermoset) and cannot be heat-welded together like thermoplastic materials.
Waterstop size (i.e. width) is determined by the expected head of water pressure to be encountered at the joint. The general rule of thumb is the larger the size of a waterstop (e.g. widths of 102, 152, 229 mm [4, 6, 9 in.]), the greater the hydrostatic pressure resisted by the waterstop.
However, it is not just size/width affecting performance—profile thickness and ribbing also play important roles with thicker products resisting higher hydrostatic pressures. Waterstop manufacturers can recommend size and type when actual project design conditions are available for review. Further, the manufacturer can provide guidance on the minimum depth of embedment the waterstop should be installed in the concrete for the expected hydrostatic pressure.
Installation failures |
The problem with waterstops is their susceptibility to improper installation or damage during the concrete placement. The following list illustrates some of the many potential installation failures for waterstops.
|
Special thermoplastic materials and profiles
For better chemical resistance to fluids, dumbbell and ribbed center-bulb waterstops are produced with thermoplastics and rubbers such as polyethylene and TPV—the latter for primary and secondary containment structures, as well as ozone contactor wastewater structures. TPV waterstops are resistant
to a wide range of oils, solvents, and industrial chemicals. Unlike PVC, TPV contains no plasticizer to leech out when exposed to chemicals and fuels.
One manufacturer reports TPV can withstand prolonged exposure to low and high temperatures (−100 to 135 C [−150 to 275 F]) without detrimental effects, but becomes very soft around 150 C (300 F), and melts at approximately 200 C (400 F). Therefore, for applications requiring very high heat resistance, metallic waterstops (discussed later in this article) should be specified and installed. For excessively cold climates, ‘arctic-grade’ PVC waterstop is specially formulated to retain its flexibility and physical properties to the range of −45 C (−50 F).
One question. When overlapping the water stop. What is the minimum overlap?
the ends should not be lapped, the ends should be welded together.
I thought that too but I’m not sure how that’d be accomplished…. Can you elaborate on this detail please….. Thanks in advance
You have to use a Splicing Iron (most waterstop manufacturers discuss splicing irons in their installation guides and other product information sheets).
is splicing iron possible to connect two waterstops with different material?
WHAT IF THE WATER STOP IS ALREADY ATTACHED TO THE CONCRETE AND DUE TO DELAYED WORKS IT IS EXPOSED TO WATER AND WEATHER THAT IT CAUSES THE WATER STOP TO SWELL AND VISIBLE CRACKS ARE SHOWN. HOW TO CORRECT THIS BEFORE CONTINUING CONCRETE POURING?
How can we connect different material class waterstops in our installation works say pvc and neoprene joining together?
What a very informative discussion about waterstop from a reputable, experienced and meticulous waterproofing consultant. Do you have writings available for copying in your website?
What continues to baffle me is why anyone believes a small piece of expansive material will do anything to prevent water intrusion through a concrete foundation wall and footing after an entire system designed and installed to prevent ANY infiltration fails. The concrete is not waterproof by nature and there are cracks and tie holes and other weak points where water will always find its way. We install this product in short 6″ or 8″ curbs/walls and it actually explodes the concrete. It is my belief waterstop can be marginally beneficial in instances where there is not waterproofing where there is not hydrostatic pressure but maybe some residual water and it may prevent some migration at the footing to wall horizontal joint. I find it hilarious that waterproofing companies require “their” version of what is essentially the same product as part of their waterproofing warranty. It’s the equivalent of saying you need a red solo cup on your boat to assure the warranty on the boat being able to not take on water.
Over lapping waterstop is not the correct way to continue through the joints, they must be welded to each other to continue through.
How to determine width PVC waterstop for internal Construction joint compared to the depth of water ?