A) VENEERS :
The layers or sheets of varying thickness from 1 to 6mm are called veneers.These are obtains with the aid of a circular rotary saw or a rotary peeling machine. They are peeled off the log by a sharp knife in a long continuous sheet by rotating the log on its longitudinal axis.They are sliced from logs of timber having extremely attractive and curly figures such as teak, siscoo, toon, mahogany , walnut, oak etc.

The process of preparing such long & continue sheets is called veneering.
The veneers so obtained are subsequently dried in kilns where the moisture contents are reduced to required value for satisfactory gluing.patterns.This process is termed as edging.
VENEERS USES :
Where light, strength, non shrinking and non-splitting properties are expected of timber.They are mostly used in the manufacture of plywood, batten , boards, laminate & for decorative facings.
B) PLYWOOD :
A board formed by gluing together three or more layers of veneers or plies is known as Plywood.

MANUFACTURING OF PLYWOOD :
The veneer are glued together usually with the grains of adjacent veneers running at right angles to each other.
The cross binding & odd number of plies make the plywood of less shrinkage, & the shrinkage stresses will be symmetrical about the middle ply which will reduce the warping tendency and will be uniform in strength in both the directions.
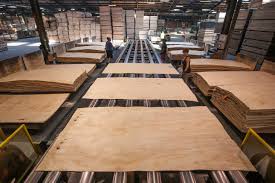
The outer ones are termed as face piles and inner one as the core or cross band.The plywood can be improved in appearance for ornamental & decorative purposes by using selected figured of certain species on the faces.
an odd numbers of thin plies of wood are placed in layers & are glued by a suitable adhesive. They are pressed to form the plywood, in a large hydraulic press under pressure of 70 to 150 degree. The thickness of plywood is generally 3 to 10mm.
To obtain strength & properties , the middle & face Plies are used of different kinds of timbers. Also strength of plywood depends upon the right choice of glue.
Thickness for plywood for 3ply is 3 to 5mm,for 5 ply 6 to 9mm for 7ply 9 to 18mm etc.
Advantages :
1)It gives better appearance as it can be formed in decorative designs & patterns by selecting figured veneers.
2)It is light in weight & has greater strength . A normal 3ply board in three times as strong as a solid board of same.
3) It gives uniform tensile strength in all directions.
4)It is obtainable in required size which is not possible for solid wood.
5) It is very easy to work & it can be bent to shapes of various designs.
6) It is highly resistant to cracking, splitting & warping as it has great stuffiness & rigidity in comparison with solid wood
PLYWOOD USES :

It is mainly used for the construction of furniture, partition, ceilings, covers, doors, windows, packing cases: for decorative purposes inside & outside surfaces of building walls & shops , buses, trains compartments etc. It is also a important material for air craft construction.
C) BATTENS BOARDS & BLOCK BOARDS :
The board having a core slab consisting of strips ,glued together between two veneers, one on either side, are knows as batten boards or block boards.
When core consists of strips of wood 8cm wide, glued together in the form of a slab, the board is called a batten board , and if the strips donot exceed 25mm in width , the board is known as block board.

The direction of grain of core battens is kept right angles to that of adjacent outer veneer.
Available in variable lengths, widths & thickness , According to requirement. They are not light but are comparatively strong.They donot split or crack easily.

USES BATTENS BOARDS & BLOCK BOARDS :

Batten Board are used for making partitions ,packing cases , floors, furniture paneling , ceiling, bus bodies, railway coaches, table tops for interior decoration etc.
Incase of block boards, other properties and uses are the same as those of batten boards. The thickness of such boards vary from 12mm to 50mm, length from 120cm to 240cm and width from 90cm to 120cm.
D) LAMIN BOARDS :
The boards having core of strip not exceeding 7mm in thickness glued together between two or more veneers are known as lamin boards.

The direction of the grain of core strips should be at right angles to that of the adjacent veneers.
They are also made on similar lines as plywood. Lamin boards are strong durable than batten boards and donot crack or split easily.

USES LAMIN BOARDS :
Lamin board are used for making partitions, packing cases and for floors etc.
E) FIBER BOARDS :
The boards made by pressing the mixture of saw dust , fibers of wood and glue are known as fiber boards.
They are also known as pressed wood or reconstructed woods.

MANUFACTURING OF FIBER BOARDS :
The selected wood converted into chips about 20mm long. These chips are put into an airtight steel vessel, called the gun & subjected to steam pressure of 30 to 60 kg/cm2.
This process softens the wood gum which keeps the wood fibers in contact.
They are than discharges by opening a valve at the Bottom.
The wood fibers will come out from the cylinder With a great force as if through a gun & will be Separated from the natural adhesive in it, due to the sudden in the from of mats of the required thickness & subjected to heat & great pressure in a hydraulic press to form solid dry sheets, known as Fiber Boards.
These board generally 3 to 12mm thickness,1.2 to 5.5m length & 1.2m in width. The weight varies from light porous variety to hard compact variety as 480kg/m3 to 1200kg/m3.
1)Insulating Boards
2)Light & Hard Boards
3) Laminated Fiber Building Boards
USES FIBER BOARDS :
1)They are used for internal finish as wall paneling , suspended ceilings and for floors.
2) They are used in making partitions and for providing finishing cover to furniture.

3)They are used in making flush doors , table tops , for bus bodies , railway coaches , prefabricated houses etc.
F) HARD BOARD :
Made from wood pulp which is compresses to make sheet usually of 3mm thick. Its face surface is made smooth and hard while back surface is made rough with pattern or cross lines.

Its width is usually 1.2m & length varies from 1.2m to 5.5m.